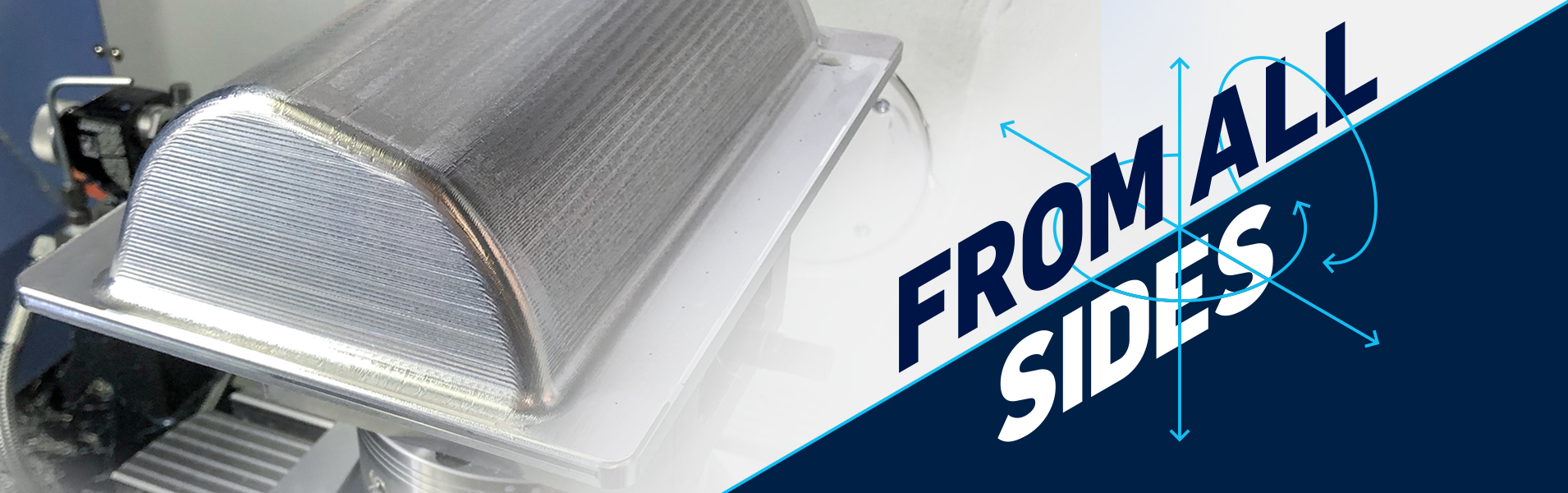
Doosan 5-Axis Productivity Revs Up Motorcycle Parts Business
Knight Design, based in Corvallis, Oregon, makes aftermarket parts for motorcycles (foot pegs) and automobiles (shift knobs). They focus on products that improve comfort, protection or performance. All the products they make are designed in their own shop and manufactured in the USA.
It can be a challenging task to keep up with all the motorcycle manufacturers out there and all of their frequent model changes. Accommodating all their customers’ needs turned the company’s 10-page website into 1,000 pages. And with the shop’s reputation for quality and innovation, customer demand kept growing. Owner Randy Knight wanted to expand capacity quickly. The obvious solution was to add some state-of-the-art machine tool equipment to the shop floor.
Randy’s top priority was quality combined with excellent price points. For that reason, he chose the technology at Doosan and the service and support at Ellison Technologies.
Challenge One: Slow Cycle Time
The company was turning out foot pegs out of 6061 and 7075 aluminum for adventure bikes, but the setup time was slowing them down. Randy shopped around for a high performance, 5-axis, vertical machining center that was designed for easy operation, even for users who had no previous experience with 5-axis machining. He was also looking for high productivity and a lot of value for his dollar.
Answer: The DNM 350/5AX
Randy found what he was looking for in the DNM 350/5AX. He could tell that the build was good, and that it was much bigger and stronger than equipment available from the competition. This differential could relate to the fact that these 5AX machines were built off of the DNM platform, which has a very deep bench. So in 2015, Randy pulled the trigger. This was his first 5-axis machine (although it is a 4+1) and it allowed him to combine different operations he had been running on multiple VMC’s. This created a much more efficient, streamlined process, along with a higher quality part. A pair of lowered foot pegs for a motorcycle used to take 2 hours with the machines he previously had. His cycle time on the DNM 350/5AX is less than an hour.
Challenge Two: Multi-Tasking
Randy was familiar with single-spindle, horizontal turning centers, but wanted something with more capability. “I was looking for a machine that could hand off parts to the sub spindle automatically to work on the back end of a part, something with a little automation so that the operator could walk away for a bit, and something that allowed us to get the parts done on just one machine.”
Answer: The PUMA TT1800SY
The TT1800SY, a dual-turret horizontal turning center with live tooling, was a perfect match for Randy’s needs. Equipped with a bar feeder and custom parts catcher, he originally made all of his motorcycle highway pegs on this machine.
Bonus: Medical Applications
Randy happened to stumble upon an inquiry from a medical device company located in San Diego that needed stainless steel pins manufactured for a fixturing application. This led him to diversify his portfolio and make his way into the medical field.
Word quickly spread in the medical segment, which brought in even more requests for parts, not just for the TT, but also the DNM 5AX. These requests had their own set of challenges. For example, there was one part made of Delrin that had some very sharp corners and complex features with close flatness callouts. It was taking an offshore shop 8 hours to run one piece. Randy’s DNM 5-axis was able to machine the part in 45 minutes.
Challenge Three: Molded Parts
Knight Design continued to expand and grow. Randy’s next target was plastic handguards and rubber motorcycle components that require a mold. The handguards are made out of either ABS plastic or Lexan material. Average cycle time on these molds is about 6 hours. “Machining of molds requires solid machine construction, higher spindle speeds for smooth finishes and an ample amount of capacity in the tool magazine to handle complex features,” Randy explained.
Answer: The DVF 5000 5-Axis
These requirements led to the purchase of a DVF 5000 5-axis vertical machining center.
Unlike the DNM350/5AX (4+1) where one axis is used for positioning and any four axis contouring simultaneously, the DVF 5000 is a true full 5-axis vertical machining center. Having all 5 axes potentially contouring simultaneously increases the flexibility of the machine exponentially. Other advantages include a fully integrated 500mm rotary table, 18,000 RPM high speed spindle and a 60-tool magazine for more storage of tools. The tool life management feature has also been a great value-added feature. Tracking the tool life on those small ball end mills and automatically reaching for the next fresh tool saves setup time on a consistent basis.
DVF Bonus #1: Automation Potential
Another feature on the DVF that excites Randy is the potential for automation based on how the machine is designed. Doosan offers a retrofittable 8-pallet automatic work changer that sits facing to the right of the machine. The operator has full access to the front of the machine and the Fanuc CNC controller. The integrated B-over-C axis table layout makes this access possible. With a background in automation, Randy has some ideas of his own for utilizing robotics, so this design feature was a big deciding factor in the purchase of the machine.
DVF Bonus #2: Hydraulics
Thru pallet hydraulics are available on the DVF 5000, in case you have hydraulic fixtures for clamping and unclamping of your part. Randy’s inventive mind envisions running air through the system to operate a unique vacuum fixture.
“The part I have in mind is a vacuum forming mold for a motorcycle handguard. The mold is made of 6061 aluminum. The inside of the mold is hollow, and we have .030-inch diameter holes drilled in the mold to aid in the vacuum forming process. The plastic-molded part will then be trimmed, using the DVF 5000. A fixture with vacuum applied to it will hold the plastic part during the 5-axis trimming process. The DVF 5000 will also produce that fixture.”
The Ellison Bonus: Service and Support
“Doosan machines are stout,” Randy said approvingly. “They’re built strong and give a lot of value for the money. That’s what attracted me to them in the first place.”
The shop rarely experiences a problem with their Doosan machines, but it gives them peace of mind to know that Ellison Technologies is standing by to keep the production line up and running. “We run a pretty capable shop, so our support needs are minimal aside from initial machine setup, understanding builder specific parameters and G-codes, or ‘how-to’ advice on configuring post processors.
“But we know that Benny Hormann and the team at Ellison will help us put the right package together for our next challenge, and technicians like Chris Westerfield will spend a lot of quality time with us on the shop floor during the installation stage for each machine.”
Growing Pains?
No matter what your product line, if you want to take your business to the next level, expand capability and increase throughput, follow Randy’s example and talk to Ellison. We’ll help you find exactly the right machine tools for you. When you’re ready, build a quote to get the process started.